What is the future for bracing buildings?
DonoBrace is an innovative product backed by the credibility of Donovan Group. It was developed based on industry experience and with expert engineering. DonoBrace is a reflection of Donovan Group’s drive towards innovation and efficiency.
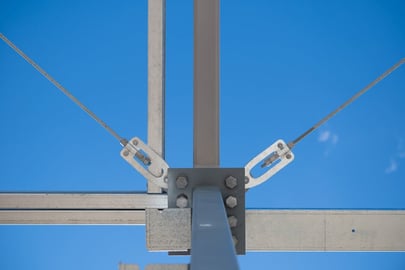